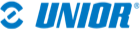
Vous pourriez avoir besoin de
Half shaft on a rear wheel drive car
The half shaft is splined into the differential assembly and runs inside the axle casing.
Half shafts, otherwise known as axle shafts, are fitted in rear-wheel-drive cars only. They give relatively little trouble during normal motoring, although they are highly stressed components.
The inner end of the shaft is supported and driven by the differential, and the outer end is supported in bearings between shaft and axle housing.
These bearings have either built-in or separate oil seals. The bearings can be ball bearings, taper roller bearings (both with inner races), or straight roller bearings which use the axle shaft as the inner race.
This video course is the best way to learn everything about cars.
Three hours of instruction available right now, and many more hours in production.
- 4K HD with full subtitles
- Complete disassembly of a sports car
When a half shaft fails, the rear wheels cannot be driven.
The main symptoms of a worn half shaft are a knock or clunk when accelerating or decelerating. The cause is wear and excessive play between the shaft and differential splines.
However, the same symptoms can be caused if the crown wheel and pinion gears in the differential are not meshing correctly, the drive-pinion flange splines are worn, or the drive-flange bolts are loose.
If you are not sure of the noise source, consult a garage. Special tools are needed to check wear, called backlash, in such components as the crown wheel and pinion.
Oil leakage, especially oil seeping from the end of the axle casing and on to the brakes, is caused by oil-seal failure. The half shaft must be removed and the seal replaced.
Removing the half shaft
Pass a socket and extension through the access holes in the flange to undo the retainer bolts or nuts.
Major work on the rear-axle assembly requires special skills and equipment available only at a garage. However, removing and checking the half shaft is relatively easy.
A slide-hammer is the only special tool needed to remove a half shaft.
Loosen the wheel nuts and jack up the rear of the car, supporting the axle casing securely on axle stands. Remove the road wheel and brake drum (See ).
On some cars it may be necessary to disconnect the brake pipe (See Checking and renewing brake cables).
Decide by visual inspection or reference to the car service manual.
If the brake pipe has to be disconnected, the braking system must be bled later (See Bleeding the brakes).
With the drum removed, you will see a flange on the end of the half shaft, either forged on as part of the shaft, or bolted on.
The shaft will be held by either a bolt-on retainer behind the flange or an inner retainer. The method of dealing with an inner retainer is described in Replacing transmission oil seals.
Most flanges have two large holes giving access to bolt-on retainers.
A socket spanner can be passed through the hole to remove the securing nuts or bolts. You should then be able to connect a slide-hammer to the shaft flange and jar the shaft and its bearings out of the axle housing.
Bolt the slide-hammer to the half-shaft flange and withdraw the shaft with steady, even strokes.
Before using the slide-hammer, make sure there is nothing else holding the retainer. The bolts holding the retainer plate may also hold the backplate.
If so, free the retainer and then refit two of the bolts to hold the brake assembly in place.
On cars with half shafts held by inner retainers, it is necessary to disconnect the propeller shaft, remove the differential pinion shaft (See ) and push in the half shaft so the C-washer retainer can be withdrawn and the shaft slid from the axle housing.
With the slide-hammer securely bolted to the half-shaft flange, start hammering steadily and withdraw the shaft slowly.
Too much force could damage the bearings, which you may plan to reuse. Always try to withdraw tight fitting components slowly and evenly, to avoid damage or distortion.
When the splined end is free, the shaft will tend to tilt; try to keep it level to avoid damaging the bearing and oil seal.
Inspecting the shaft, bearings and oil seal
Take the half shaft to a workbench and (unless it is obviously broken) examine it carefully along its length for signs of rubbing or 'high spots' recognisable as shiny spots on the metal. Check it with a straight-edged rule for distortion.
Never hammer a slightly distorted shaft in an attempt to straighten it. It can only be straightened in a press. If distortion is severe, a new shaft must be fitted.
Pay particular attention to the splined ends. They must be in perfect condition, with no sign of wear.
Clean the bearings in paraffin and inspect the balls and races for pitting.
A badly worn bearing will run roughly and, in extreme cases, feel sloppy.
After cleaning, lubricate the bearing with fresh oil, spin it close to your ear, and listen carefully. Rough running will be clearly audible as a grating sound.
It is, however, advisable to renew bearings automatically whenever a shaft is disturbed.
Bearing removal and replacement is a precise operation and usually requires a hydraulic press. It is best left to a garage.
Bearings can be hammered off and drifted back on, but there is a danger of distorting the shaft.
Bearings with integral oil seals are usually retained by a collar or ring which has to be split with a chisel before removal.
It is better to have the job carried out professionally.
If the seal is not integral with the bearing (on some older cars) it can be prised out and replaced before refitting the half shaft.
Clean and lightly grease the whole shaft and push it gently into the axle casing until you feel the end come up against the differential side-bearing splines.
Move the shaft around until the splines engage, then drive it fully home with a soft-faced hammer against the flange centre.
Do not hit the flange on its edges, or with a steel hammer, or it could break.
Reassembly of the flange, brake drum, brake hose and wheel is the reverse of the removal.
After refitting the half shafts, lower the car on to its wheels, check the rear-axle oil level and top up if necessary.